Manufacturing in the times of COVID
Everything has changed, everything will continue to change, the world is adapting, we will never go back to the same as before. From global and local impacts, as well as the accelerated migration of processes to Industry 4.0. We will talk a little bit about everything.
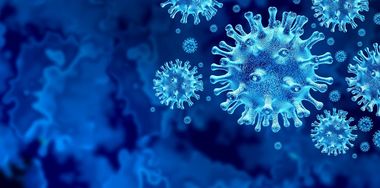
It is a reality, all industries have changed, manufacturing has been strongly impacted. Health and Safety, Quality, Productivity, Supply Chain, Manufacturing Costs, etc. Leaders within manufacturing today have to adapt to the new changes, understand, plan and strategize based on these changes and, above all, correctly cascade these strategies so that an entire team is really pointing in the same direction and can move down that path as quickly as possible.
The complication for manufacturing because of Covid has many edges. One of them is due to the adjacent globalization of manufacturing processes. Today many companies, most probably, have global sourcing of their raw materials. The pandemic affected the whole world, the complicated thing for manufacturing is that it affected at different times, causing production stoppages and problems for the reactivation of production. Today, for example, the shortage of semiconductors is strongly affecting the manufacturing industry, primarily the automotive industry, causing production stoppages in manufacturing plants in different parts of the world. The supply chain has been affected and impacted on a large scale, causing a disproportionate increase in transportation costs. Companies have found themselves with the need to expedite and increase shipping frequencies, move and completely change inventories, etc. It is a total restructuring process that is taking place in manufacturing because of Covid.
If we analyze the impacts in a local way, we can say that the changes in manufacturing start from the moment a company's workers travel to start their working day. In cases where the company provides transportation for its employees, additional hygiene and safety measures have been adapted to avoid disease transmission, which can lead to additional costs either because the transportation company increases the cost of its service or because the client company absorbs all the additional costs for sanitation and hygiene of the transportation system. Discipline has also been impacted. It is now more important than ever as leaders to set an example in the use of personal protective equipment. All employees using company transportation, those using public transportation, and everyone on company premises will be asked to be aware and disciplined in the use of goggles and masks. How do we do this? By creating the right mindset in all members of the organization, fostering mutual respect and care. Here the strategies of leaders and companies may vary, but the objective is the same. Discipline and respect, towards them, towards their colleagues, towards their families by the simple fact of using constantly and at all times the additional protective equipment to protect us from the transmission of the virus.
Productivity and the way we measure it is one of the areas that probably has been and continues to be impacted the most in the manufacturing world. Additional items such as purchasing canisters with lids for production lines, tissues on lines, visual aids on lines, visual aids at pedestrian access, visual aids in offices and boardrooms, creation of behavioral protocols, purchase of specific and additional face masks, additional purchases of protective eyewear, balancing workloads to achieve additional physical distance, changing the layout of a line or plant, hiring personnel specifically to audit virus transmission issues, promoting teleworking are just a few of the things, to name a few, that have totally changed in the manufacturing world following the advent of COVID-19. It is very likely that the statement "every company in the world is promoting teleworking or home office" is a correct statement in these times. All jobs are essential in manufacturing, they exist for a reason, however, it is a reality that the physical presence of many of these jobs in manufacturing plants is not a necessity. We have known this since before the pandemic, in fact we have known it for a long time, since technology allowed us to have video conferences, since email and the computer and the internet became the main work tool for many jobs, however, it has never been promoted as it is now. When we think about it, it is probably even absurd that this had to happen to really adopt a working model and scheme according to the technological and virtual times we live in. This also brings us to the fact that many business trips were canceled, will continue to be canceled, and we will likely find that they were never really necessary. This is not to say that all business travel will be cancelled or have to be cancelled forever, certainly nothing will ever replace personal interaction and the benefits we can achieve from it, nothing will replace the way we can read people's behavior and reactions in a face-to-face meeting, nothing will replace the effectiveness with which physical interaction at work promotes the transmission of leadership behaviors, attitudes and work culture. The amount of work travel has changed forever, forcing organizations and company leaders to redefine when physical interaction is really necessary. Very specific courses where physical presence is required, negotiation meetings, integration meetings, etc., are examples of situations where it will be important to maintain a physical presence. In short, business travel will never again be as frequent and necessary as it once was.
Another major impact? Manufacturing costs have changed dramatically. Some for the better, most probably for the worse. Some additional costs caused by the virus are for example the purchase of antigen tests to detect the virus in a company's population, adjustments and changes in tables and industrial canteen services, purchase of hand sanitizer gel dispensers, which we now see everywhere, purchase of towels and liquid disinfectants for desks or workstations, purchase of infrared thermometers, purchase of mats and liquid disinfectants for shoes, purchase of masks for employees, purchase of additional eyeglasses, purchase of visual aids, even hiring additional people at the entrances to measure temperatures and ensure protocols. Creating the mentality of protection and prevention of transmission also has an impact on costs, as more frequent hand washing is now promoted, which will also lead to buying more hand soap, buying more paper to dry hands or buying air drying devices, which in turn will lead to additional maintenance costs to prevent or fix malfunctioning of these dryers, etc. These are just a few examples of additional costs that, although not very expensive, when projected by the number of people in a company, become very considerable and significant.
Now imagine the economic impact of those companies that, in order to reactivate, had to change their layouts or had to completely rebalance their production lines in order to respect the healthy distance. Imagine the associated costs of those companies that have no choice but to accelerate the integration of emerging technologies, such as virtual or augmented reality, such as additive manufacturing, such as cognitive automation and remote analysis of their ecosystems, as well as accelerating the incorporation of interconnectivity and interoperability tools that will become the basis of Industry 4.0 for manufacturing processes.
As we can see, many things have changed in manufacturing in the wake of the SARS-COV-2, and here we only mention a few things. We cannot wish to go back to the way things were, because we will probably never go back to the way things were before, the way now is to adapt. At Quality Accent we firmly believe that innovation will never cease to be the best tool to combat manufacturing impacts. Leading by example should be the norm to follow in order to create the work culture and new standards that are desired and needed in manufacturing in the times of COVID in order to return or increase the profitability of the manufacturing sector.
Continue to take care of yourselves and extreme precautions, there is still a long way to go before we can feel safe again.
Share
Te Recomendamos / We Recommend
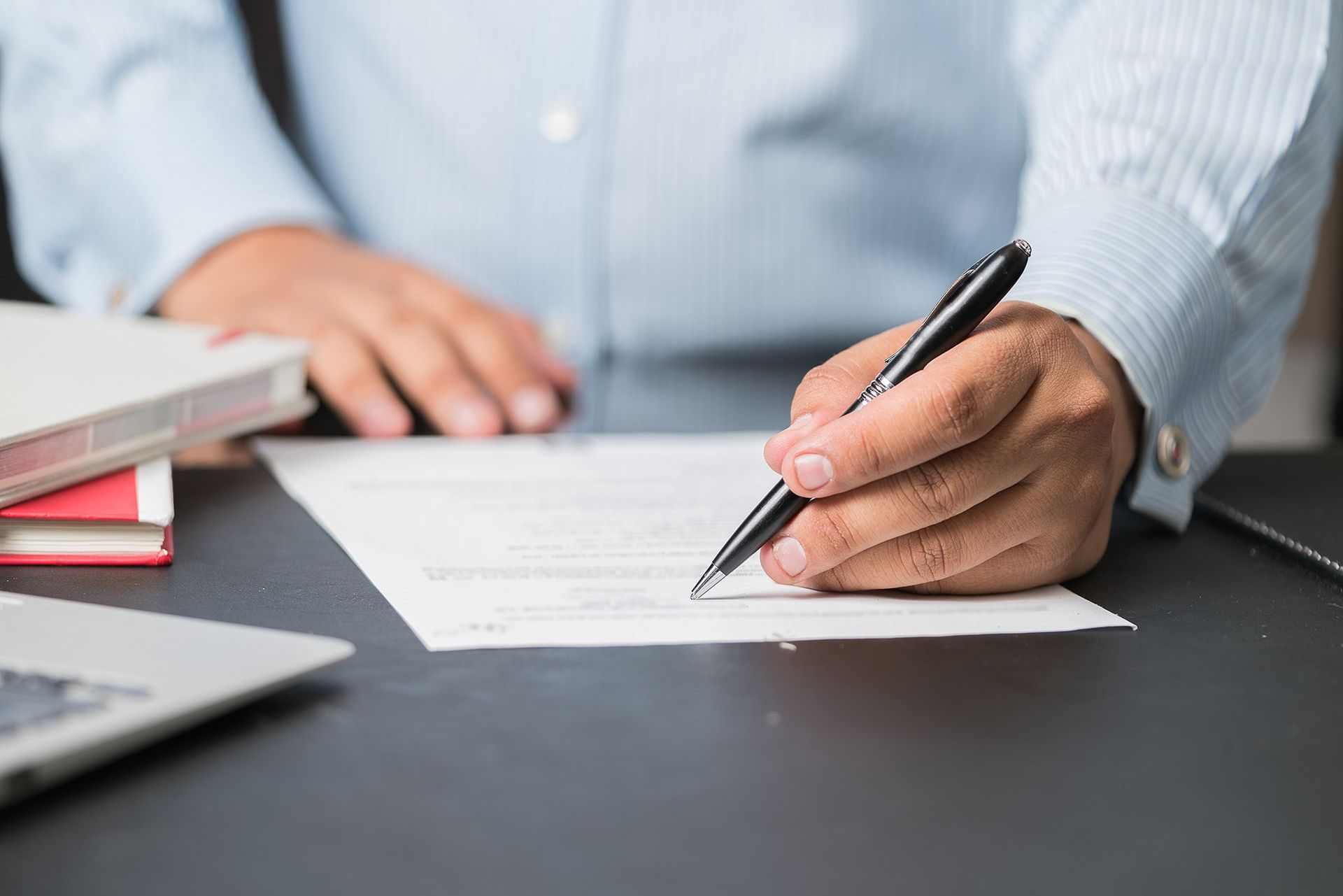
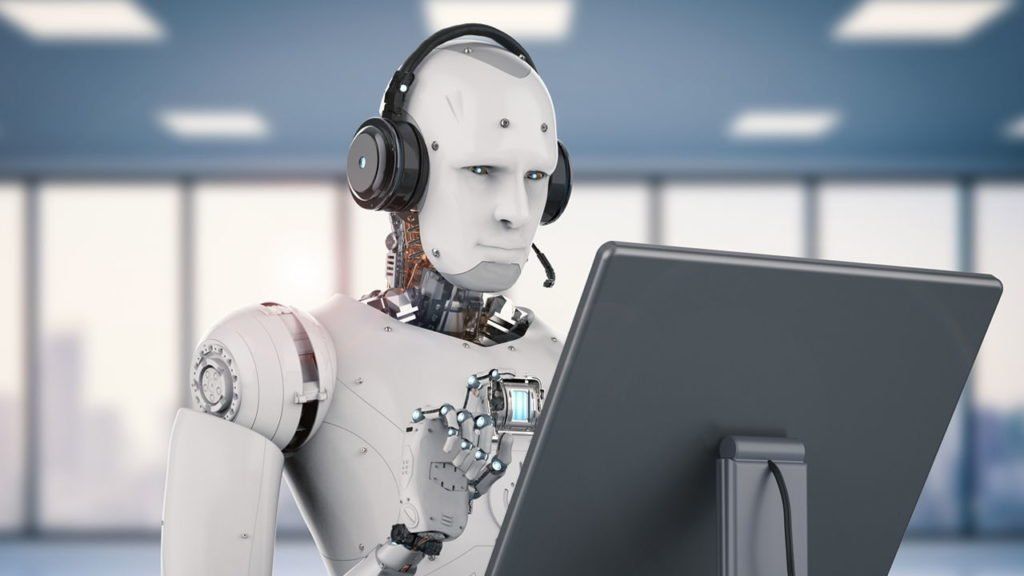
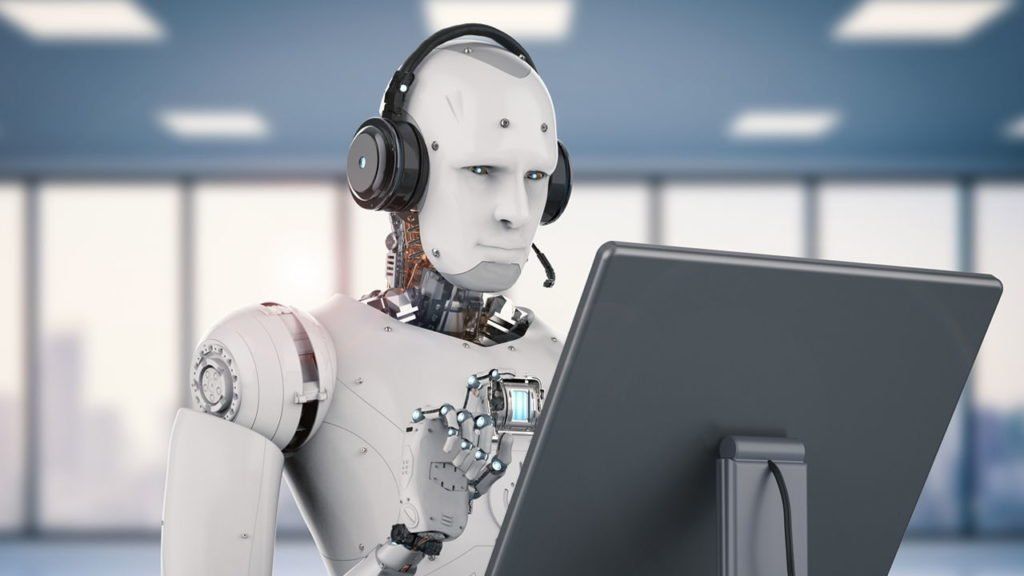